Operational Excellence – 10 Core Principles for Achieving Excellence in Business Operations
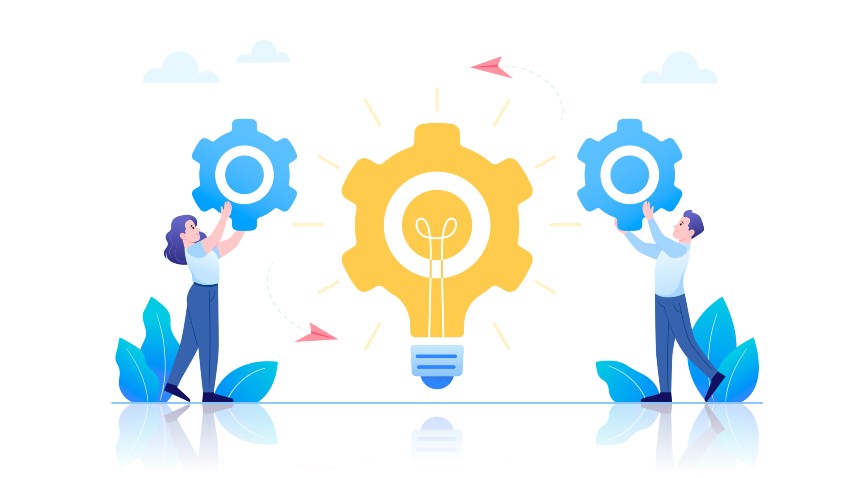
Running a business is one thing, but achieving excellence in operations is another ball game altogether. Operational excellence is something that every business aspires to achieve.
What does operational excellence look like?
What are the tactics behind achieving operational excellence?
Is operational excellence a must for every business?
This blog answers all of these questions and provid
continuous improvement initiatives
es details on what is operational excellence, ways to achieve operational excellence, methodologies, and tools that help businesses achieve operational excellence.
Understanding Business Operations
In the corporate world, there are several phrases that are used repeatedly but are rarely understood. These classic buzzwords are used by everyone without really thinking about the real meaning. One such example is – “business operations”. We must have heard this term a thousand times now, but what does it actually refer to? Business operations is a broad term used to define a range of business activities undertaken on a daily basis to keep the business running and generating revenue. The nature of business operations varies hugely from one company to another.
For example, the typical business operations in an Online store may include-
- Marketing
- Order management
- Web design and development
- Sales
- Inventory management
- Warehousing and fulfillment
The specifics of business operations are individual to each business, some aspects are shared across the board. The 3 main components of business operations are – Processes, Human resources, technology, and equipment. Processes are the most critical components of business operations, they are important for the survival of the business.
Efficient processes ensure business productivity and profitability. Human resources are the ones that run business processes. Having a skilled and competent workforce is important for smooth business operations. Finally, the right technology or tools are required to keep the business running smoothly.
Accounting and finance, Human resources, Marketing and Sales, Manufacturing, Supply Chain, Customer Service, and Regulatory Compliance are some examples of business operations.
Business operations can be broadly classified into 4 types –
1. Production:
Production operations are concerned with the creation of goods or services.
2. Financial:
Financial operations are concerned with managing the money and resources of the business.
3. Marketing:
Marketing operations revolve around selling products or services.
4. Human resources:
Human resource operations are concerned with managing the workforce.
What is Operational Excellence?
How to Define Excellence in a Business?
The definition of operational excellence is a methodology of striving for efficiency throughout the organization’s processes. We can also define operational excellence as the approach to business management that focuses on continuous improvement across all aspects of the business and within all the business processes by creating a culture that unites management and employees towards better business outcomes and change management.
Excellence in operations enables every member of the organization to see the flow of value to the customer and find timely solutions to issues before they disrupt business operations. Operational excellence begins with a culture shift within the organization where all leaders and employees work towards creating a quality product and providing great customer experiences.
Another definition of operational excellence is a state in which every employee can see the workflow and adjust the flow before it stops flowing. It essentially means that the flow of business operations must not be interrupted at any cost for operational excellence. This definition is easy to understand because it applies to all levels of employment.
Moreover, every person should know that there should be a visible product flow or information in their area, which enables them to take necessary action when the flow tends to be abnormal. Visibility into the process flow also equips employees with the ability to solve issues that arise without any intervention from their superiors.
When posed with the question of their idea of operational excellence, each business comes up with a different definition. Some consider being the best globally as a measure of operational excellence, while others may consider being excellent at everything they do as a measure of operational excellence.
However, when we define operational excellence, it is better to have a specific, measurable, and time-bound definition, which will help businesses achieve excellence in operations.
Businesses that implement Operational Excellence methodologies define leadership and workforce roles clearly, and how they work together to improve business operations. Guided by these methodologies, employees at all levels can initiate change and drive toward efficiency, effectiveness, and agility.
Operational excellence must not be viewed as a set of activities that businesses perform, rather it is a mindset that must be present within management and employees. It must be considered as a philosophy that embraces problem-solving and leadership as the key to continuous improvement.
How to Achieve Operational Excellence?
Before we get into the guiding principles for achieving Operational Excellence, let us first understand the building blocks for building a culture of operational excellence. The key aspects of operational excellence are strategy, organization structure, processes and systems, and products and services.
Operational excellence in strategy is enabled by performance management, organization structure is enabled by leadership and culture, process and systems are enabled by continuous improvement, and in products and services is enabled by risk and quality management.
Performance management takes a balanced scorecard approach to focus on all aspects of the business, rather than specific areas. Customers, internal business growth, and skill improvement are considered in performance management. Key performance indicators, an important part of performance management, guide the management on which areas of the process need to be evaluated.
Continuous improvement means that the organization is centred around its processes. Continuous improvement is a well-designed and efficient support system that is based on Six Sigma, Lean manufacturing, and Kaizen principles. Leadership and culture involve attracting and retaining the right talent in the organization. Creating a culture that encourages the desired behaviours and continually developing leadership competencies is the main aim of leadership and culture.
Another important aspect of operational excellence is improving team performance. Building high-performance teams by empowering, educating, and engaging employees requires a rich and inclusive work culture. This can be achieved by establishing strong values and principles around the work culture, creating leadership roles, and continuing competence development.
Principles of Operational Excellence
The 10 guiding principles of Operational excellence are derived from the Shingo Models. The Shingo Model is a set of principles used to build a culture of excellence in the organization. These core principles are categorized as culture enablers, continuous improvement, and enterprise alignment.
Let us look at these core principles for achieving Operational Excellence.
1. Seek perfection
As the name suggests, this principle focuses on achieving perfection in each task. However, this principle is met with resistance because most people think that perfection is not possible. For tasks that have measurable outcomes, perfection can be achieved. This can be achieved by setting high standards within the company that employees are encouraged to achieve. Striving to simplify your work without compromising on quality, or looking for long-term solutions for an issue are examples of setting high work standards.
2. Stay focused on the process
A natural human tendency is to blame others when things go wrong. Very often, the reason for failure is in the process and not in the individual. Even a skilled or talented employee would not be able to produce consistent results when they are working in a poor process. Instead of pointing fingers at employees when an issue occurs, you should assess which part of the process is causing the issue and try to resolve it. Once this assessment is done, you can tweak the process to get the desired result.
3. Respect for all individuals
Each stakeholder involved in the process must be respected for their potential and worth. It is not enough to just show respect for others, you should explicitly show it to them. An effective way to show respect to team members is to involve them in all initiatives for improving department performance. This way, they are not only engaged effectively but also feel empowered and motivated to participate in continuous improvement initiatives. Practice a culture that engages every employee, from the CEO to the shop floor staff.
4. Practice scientific thinking
Continuous experimentation and learning are important for innovation. A scientific rationale must be applied to identify what works and what doesn’t. Encouraging employees to think innovatively and explore new ideas is a great way to engage them.
5. Assure quality at the source
Total quality is possible only when all parts of the process are executed optimally. A well-planned and organized process makes it possible to identify potential problems immediately. As and when a problem is identified, it is important to stop and fix it before moving on, so that quality is assured at the source.
6. Practice humility
Great leaders are often humble. Humility is what differentiates a leader from a “boss”. Having a humble leader encourages team members to admit their mistakes and seek ways to rectify or improve upon them. A humble leader is willing to listen to and accept suggestions from all employees, irrespective of their position within the team/company.
7. Align individual goals with organizational goals
It is not enough if you apprise the employee about organizational goals on the first day of their employment. You need to constantly remind them of the purpose of their work so that they have a clear understanding of why the company exists, where it is going, and how it will get there. Reiterating organizational goals constantly enables employees to align their goals and actions with the overall company goals.
8. Create value for customers
To add value to customer service, you need to completely understand the customer’s expectations. Value is simply the price that a person will pay for. Companies must work hard to ensure that their customers’ needs are understood and met adequately. A company that ceases to deliver vault to its customers is not sustainable.
9. Flow value and pull value
The ultimate goal of every organization is to offer maximum value to its customers. Uninterrupted processes and workflows can lead to inefficiencies and waste. Assessing customer demands is important to determine the value you can provide to them. Value to customers is maximized when it is created in response to real demand and a continuous and uninterrupted flow.
10. Think systematically
For a process or system to work effectively, all the interconnected parts that make up the process must work together. Understanding how each task that makes up the process is linked to other processes, allows stakeholders to make better decisions. Limiting the vision of your company must be avoided to ensure that your organization grows sustainably. Any obstacles that come in the way of achieving organizational goals or the flow of information must be eliminated at any cost.
Operational Excellence versus Continuous Improvement
While we talk about Operational Excellence, it is important to distinguish between continuous improvement and operational excellence. Continuous improvement is an ongoing effort to improve an organization’s processes, products, and services. Efforts towards continuous improvement take place incrementally over time, rather than instantly through some breakthrough innovation.
Organizations that pursue continuous improvement are more likely to build or continue to maintain these improvements. Although continuous improvement is important, it cannot work alone to improve business outcomes. As the organization continues to refine its process, product, or service, it needs a way to grow. This is where Operational Excellence comes in.
Operational excellence is a culture that embraces certain tools and principles to create sustainable improvement within an organization. Operational excellence is achieved when every member of the organization can see the flow of value to the customer. It is used to improve value as well as the delivery.
Operational Excellence is not just about reducing costs or increasing productivity, it is also about creating a company culture that will allow companies to build valuable products and services for the customers for achieving long-term sustainable growth. Operational excellence is a journey that is accomplished with the right tools applied to the right process. An ideal work culture is created where employees are provided in a way that enables them to stay motivated and empowered.
Continuous improvement aims to identify the immediate and discrete changes that need to be made to keep the business competitive. By regularly evaluating processes, workflows, and ongoing projects, teams get a better understanding of why something that would have worked at one time no longer delivered the desired results later. Operational excellence is a broader strategy that shapes long-term goals, impacts company culture, and focuses on sustainable solutions.
Process Excellence versus Operational Excellence
Operational excellence is all about improving business processes, but is it the same as process excellence? While both process and operational excellence aim at producing excellence, their scope is different. Process excellence focuses on a single process or workflow. Isolating the process makes it easier to dig into one area of work, and then solve the issues in that specific area of the process. Operational excellence on the other hand includes process excellence initiatives but also considers the relationships between processes.
Consider the finance team for example. The team may have an overarching goal of attaining operational excellence across the department. To achieve this, managers may be tasked with different processes such as procurement, accounts payable, accounts receivable, and expense reimbursement.
Optimizing individual processes within these departments is also part of process excellence. Once each process is optimized, an operational excellence perspective would look at how these processes impact and interact with each other, how data is shared between them, and whether there are any instances of duplicate work or waste. Bridging process gaps, dissolution of silos, and solving any new problems that occur when new apps and systems are installed, are part of operational excellence.
Why is Operational Excellence Important?
The most obvious reason why businesses strive to achieve operational excellence is to stay competitive and deliver value to customers. While pursuing operational excellence, waste, and redundancies are eliminated, and those resources are channelled back to adding value to customer service. Operational excellence is typically focused on delivering value to the customer.
Here is why operational excellence is important for the business –
Value flow to customers
Operational excellence enables businesses to deliver what customers demand by creating a value stream. A value stream refers to the processes and initiatives that an organization creates to deliver products and services the customers need in the time it takes to meet that demand.
Lower costs and increased revenue
Organizations that adopt Operational Excellence to their business processes will benefit from its data-driven evaluation and evaluation approach. Operational Excellence tools assess and measure at each stage of the process to help lower costs and increase revenue.
Reduced waste and sustainable profits
Redundant and wasteful steps in business processes are eliminated by adopting operational excellence. These steps affect the overall productivity of the business, hence, eliminating them gets rid of additional costs associated with them. Operational excellence helps in the identification and elimination of waste so that organizations can achieve success and objectives sustainably.
Improved customer satisfaction
Operational excellence aims at adding value to the business processes that help the organization attain its vision and mission. It makes sure that every function in the business adds value and fulfils customers’ needs.
Higher quality and productivity
Operations excellence helps streamline the business process to enable continuous improvement in their organizations. This ensures that organizations have good productivity and deliver high-quality products and services to their customers.
Better partnership with stakeholders
Operational Excellence emphasizes transparency and effective communication among stakeholders and business partners, which establishes a smooth business environment that drives growth.
Empowered and efficient workforce
Empowering employees is one of the key focuses of Operational excellence. Involving every member of the organization and making them aware of the steps that need to be taken to deliver optimum productivity is important for operational excellence.
Resilient and adaptable organization
Achieving operational excellence makes the organization future-proof. Any events or episodes that affect business goals are eliminated using Operational Excellence tools. Operational Excellence ensures that businesses are resilient and adaptable.
Methodologies in Operational Excellence
Achieving excellence in operations requires a good amount of planning, the right resources, and channeled efforts. Almost any type of business can achieve operational excellence by following any one of the methodologies listed below based on the nature and requirements of their business.
Shingo Model – for building a sustainable culture of organizational excellence
This model emphasizes the importance of understanding how organizational excellence works, and also how it is achieved. This model breaks each system into smaller parts and focuses on identifying the KPIs and leading indicators for measuring the success of each part. The 10 principles of achieving Operational Excellence mentioned above are derived from the Shingo Model.
Lean methodology – aims at reducing waste in a process
The Lean methodology focuses on reducing the waste in a process to zero and delivering perfect customer value. The Lean methodology is closely related to the Shingo methodology in having its origins in the automotive production process. John Krafcik is credited with having coined the term “lean” in his article titled “ Triumph of the Lean Production System”.
The key concepts in the Lean management methodology are listed below-
- Value stream – This includes all the tasks, actions, and workflows required to complete the product successfully.
- Flow – This indicates the relationship and momentum between all the elements of the value stream.
- Pull – The ability to build the product exactly the way the customer wants and deliver it exactly when they want.
- Transparency – Transparency across all stages of the process ensures that everyone involved in the value stream has visibility and access to relevant information.
- Perfection – The relentless pursuit of improvement.
Kaizen – continual change for the better
The Kaizen approach is also similar to the first two models, and it is a Japanese term meaning “continual change for better”. Originally applied to assembly lines in auto manufacturing, Kaizen principles have since been applied to a broad range of initiatives and activities. This approach to operational excellence is based on 5 principles mentioned below-
- Understand the customer to create value
- Eliminate waste at every step of the process
- Engage change where work happens
- Be transparent and data-driven
- Empower people
Six Sigma – Focus on minimizing or eliminating process variance
This methodology is the most recently developed one among the others. It was developed in the 1980s by an American engineer named Bill Smith working at Motorola. The name, Six Sigma, is derived from the standard deviation arch of a normal distribution model that this model refers to.
The primary Six Sigma methodology is called DMAIC – which is an acronym for Define, Measure, Analyze, Improve, and Control. This is a five-step approach to problem-solving that breaks down each step into a series of tasks and deliverables.
- Define – Identify the problem, all the stakeholders, customer value, and improvement plan clearly.
- Measure – Determine the key metrics and validate their measurements.
- Analyze – Identify causes of inefficiencies or problems within the process.
- Improve – Develop and implement a solution plan.
- Control – Build processes and standards around the newly optimized process.
The main difference between Six Sigma and Lean methodology is that the former focuses on eliminating variance and reducing waste.
Businesses can choose from any of the above methodologies to achieve Operational Excellence in their processes. The nature of business operations must be considered while choosing the methodology appropriate for your business.
End-to-end workflow automation
Build fully-customizable, no code process workflows in a jiffy.
4 Tools for Achieving Operational Excellence
Now that we have discussed the methodologies that can be followed to achieve Operational Excellence, let us now get introduced some of the popularly used tools to implement these methodologies. Here again, the choice of the tool depends on the nature and scope of business operations.
1. Process Mapping
A process map is a business operation essentially the blueprint or visual representation of a process or workflow. Process maps can be of the “as-is” method or the “to-be” process. These maps can be created by using an application or drawn by hand. Standard flowchart symbols are used to represent various components of the process.
2. IT-business team alignment
Almost every business process is a complex stack of software tools and apps that are managed by the IT team. It is therefore important to ensure that these teams are aligned and they work together to solve business problems.
3. Low-code software
The most effective way to eliminate dependency on IT is to use low-code software. Low code or no code software is primarily made up of visual elements that are used to create workflows. Such software requires fewer coding resources to implement, maintain, and use. Teams can use low-code software to solve problems quickly using the IT-sanctioned toolbox that can be accessed via a visual user interface. Such software enables businesses to stay more agile without adding to the IT workload.
4. Automation
Automation technologies help businesses develop process flow, eliminate waste, and generate additional value for customer experience. A low code workflow automation software like Cflow automates processes at task, process, and workflow levels. By automating repetitive tasks in a workflow, response times can be improved and the need for manual slogging can be eliminated.
Challenges in Achieving Operational Excellence
Achieving operational excellence may seem very easy on paper, but the real challenge crops up when you try to achieve it. There are several hurdles that may come your way while achieving Operational Excellence. Here are some of the common challenges that businesses face while implementing methods to achieve operational excellence.
1. Inability to adapt
The lack of willingness or the inability to adapt to changes while implementing process improvements can cause stall Operational Excellence efforts.
2. Detachment of employees
When employees are not sold on the idea of achieving operational excellence or the means to achieve it, they detach themselves from ongoing process improvement activities. Their detachment can hinder their ability to achieve operational excellence and cause much confusion in understanding their role in the overall strategy of the business.
3. Large data volumes
Data-driven decisions are no doubt important for the business, but there is a limit to the volume of data that can be handled. Leadership cannot make decisions based on the data if it is too complex or voluminous to understand.
4. Slow progress
It is very common to see team members getting disinterested in Operational Excellence initiatives when the progress is too slow. Hardworking employees want to see rapid progress. Slow progress demotivates and discourages employees from working toward operational excellence.
Automation and Operational Excellence
One of the operational excellence tools that businesses can use is workflow or process automation. Process automation streamlines the workflow by eliminating redundancies and accelerating the process cycle. When we go for low-code or no-code automation software, it becomes even easier to achieve excellence in operations. Choosing the tool that an organization uses to achieve operational excellence is an important decision.
Workflow automation software like Cflow is a one-stop solution that addresses all the requirements of operational excellence. The visual workflow builder in Cflow can be used to build workflows for key business processes within minutes. Even people without any technical background can easily create workflows by simply dragging and dropping workflow elements. Users can customize workflows as per unique business requirements.
Real-time reports and analytics from Cflow, enable leadership to stay informed about the progress of each task. Achieving operational excellence is a breeze with a no-code workflow automation platform like Cflow. By automating repetitive tasks in a workflow, operations are streamlined and the process is rendered highly effective. Cflow brings consistency and transparency into business processes so that all stakeholders are informed about the progress of tasks.
Conclusion
While all organizations strive for operational excellence, it is important to support Operational Excellence methodologies with the right tools and software. Relying on tools and projects alone to achieve excellence in operations is not enough. Embedding operational excellence principles and methodologies deep into the culture of the organization and using appropriate tools for implementing these methodologies is the need of the hour. Involving management and employees from the start to understand and implement Operational Excellence principles is a healthy practice for building a sustainable business.
Cflow is a workflow automation tool that helps implement operational excellence principles effectively. To explore deeper, sign up for the free trial of Cflow today.
What would you like to do next?
Automate your workflows with our Cflow experts.