From Mediocrity To Excellence: Achieving The Process Excellence Through Automation
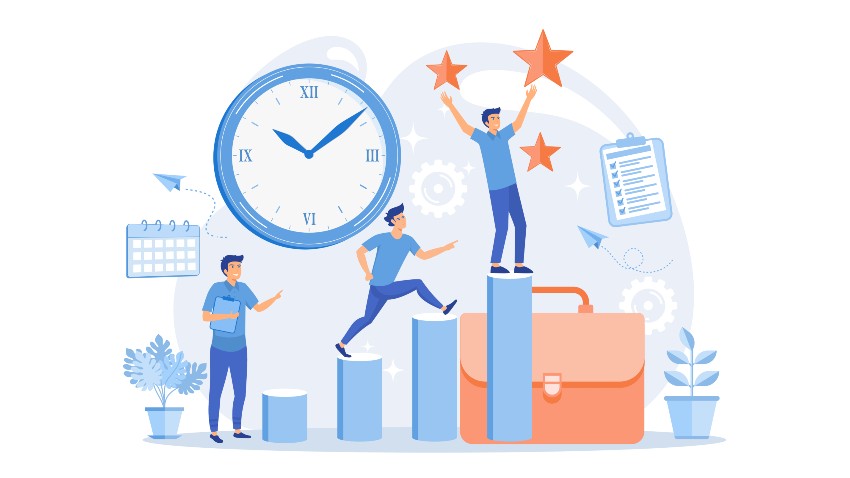
The success of a business is measured by its productivity, growth, sustainability, and profitability. The management knows that they must deliver consistent quality output if they want to crunch these metrics for success. The key to quality business outcomes is to set up excellent, effective, and efficient processes.
Process excellence is a win-win for all the stakeholders, leadership and owners reap the profits, while customers benefit from the value addition of business process excellence.
In this space, we explore process excellence framework, ways to build a process excellence strategy and process excellence tools for your business.
Understanding Process Excellence
So, what is process excellence?
Business process excellence or process excellence is a method for improving the performance and efficiency of business processes. To obtain process excellence, a process is examined, changed, and tested to fulfill the objectives.
Another process excellence definition is that it is a strategy for adapting business processes to maximize productivity and efficiency. A process excellence strategy helps set quality standards against which process performance is measured.
What are the factors that determine process excellence? Achieving business process excellence depends on several factors that vary in each business. But in general, these factors determine process excellence.
- Efficiency
- Accuracy
- Speed
- Visibility
- Productivity
- Visibility
- Security and Compliance
- Consistency
- Alignment with business strategy
- Ability to meet targets and achieve goals
Process excellence emphasizes that there is never a final level to achieve, there is only continuous monitoring of the process. As long as a process is in place, there will always be opportunities to streamline it, improve upon its efficiency, and produce better results.
Process excellence activities are mainly concerned with the elimination of bottlenecks, and redundancies, and fixing issues that may arise during process run time. Businesses aim for process excellence because it helps them improve how they create and deliver value to their customers, stakeholders, and customers. Organizations use process excellence to identify opportunities for improvement and to create innovative solutions.
Components of a Process Excellence Framework
Process excellence is a continuous activity that requires organizations to frequently revisit their process maps and reassess processes in response to changing circumstances. There are 5 main components that an organization must include in its process excellence strategy to achieve long-term success.
Ownership and alignment
Knowing who is responsible for processes in your organization and defining their roles clearly is a must for achieving process excellence. There are hundreds of processes that run an organization, yet most of the time there is no clarity on who is responsible for what in these processes. As a result, no one feels that it is their responsibility to improve the process.
For instance, the manager of a minimarket is responsible for ensuring goods are delivered on time, but are they also responsible for managing waste generated in the store? Clarity in such matters is important to achieve process excellence in an organization. A process map helps identify all the processes in the company, see the relationship between them, and allocate responsibility for each of the tasks in the process map.
Continuous process improvement
Processes are mainly affected by outside events, which require constant monitoring of processes to identify opportunities for improvement. A technology company, for example, decides to introduce a policy that lets employees work remotely as a result of the pandemic. To support this transition, the onboarding process, remote work request processes, and IT processes must be upgraded to ensure that the workflows are still relevant and effective.
Definition, documentation, and understanding
Written documentation and instructions are a must for achieving process excellence. Documents create consistency across the board and make it clear how processes are organized and set up.
For instance, the dispute verification process in an insurance company involves several escalation stages, starting from initial complaint to resolution. Creating a clear documented explanation of the protocol and why the organization resolves disputes this way, helps everyone involved in the process to understand the workflow and the logic behind each stage in the process.
Performance management
To spot issues in the process workflow, you need a complete understanding of the impact of the issue and the way to deal with these issues. Process excellence helps organizations to identify the issues in the processes and fix them effectively.
For example, in a fast-growing financial firm that still uses a lot of manual processes in managing payments, implementing a process improvement methodology for streamlining payments helps identify problems and introduce solutions.
Development of technology and automation
The introduction of business process automation software allows companies to automate processes for managing processes more effectively. For instance, a school board decides to automate its payroll and onboarding processes. Digitizing these workflows boosts efficiency and saves staff from labor-intensive work like collecting data or managing approvals.
5 Steps to Achieving Process Excellence
Businesses need to adopt a structured and well-organized approach toward process excellence to achieve consistency, visibility, and accountability across processes. The steps to achieving process excellence are listed below:
1. Defining the target process
The first and most important step is to identify the process that will improve by implementing process excellence methods. Some processes may be working fine, and may not benefit from implementing process excellence measures. It is better to exclude these processes from process excellence initiatives.
The overall goal of process management initiatives is to create optimized and orchestrated versions of the processes that happen within the organization. The best approach to process excellence is to highlight a single process and get it right before moving on to the next process.
2. Mapping the “as-is” process
For optimizing the target process, you require a detailed map of the process that maps the key steps. The as-is process map must highlight the following –
- The starting point or the trigger for the process
- Outcomes or results of the process
- Inputs required – like information, time, effort
- Systems for running the process
- Handoffs – mainly instances where work changes hands
- Integrations – Points at which data crosses app or system barriers
Commonly followed process mapping methods include- flow charts, process maps, BPMN diagrams, flow diagrams, etc.
3. Evaluating the as-is process
Improving the as-is process requires a thorough understanding of the process flow. For this, you need to gather some data on its current performance. The data points can be gathered based on the following questions.
- Is the target process structured or unstructured?
- What is the primary performance metric or the KPI for the process?
- Is there a mechanism in place for measuring this metric?
- To what extent is the process meeting the KPIs?
- Which elements of the process contribute to its performance?
- What are the improvement areas of the process?
4. Create the to-be process
The optimized or to-be version of the process needs to be mapped. What are all the improvements that the new version of the process must include? The cross-team collaboration required for implementing the to-be process also must be identified before the implementation.
5. Test the New Version of the Process
An effective way of implementing the to-be process changes is to run the version on a limited scale or with only a few users. While implementing the changes, you need to keep an eye on the data and collaboration silos that may appear. Data silos commonly occur during the implementation when information is shared between people, tasks are handed off from one party to another, or where data moves across system boundaries when apps or databases are integrated.
6. Implement the to-be process
Train the team and all other stakeholders on the new to-be process to prepare them for the use of the system. If the new version of the process introduces new apps and systems, make sure that the team is appraised of the usage of new systems.
7. Review the results
Once the to-be process is implemented, you need to determine if the version of the process meets the performance requirements. In case the process does not meet the requirements, the team needs to assess the reason why. Revise the process and try again until the expected target is achieved.
8. Monitor and modify as required
The teams need to ensure that they have enough resources to gain deep visibility into the performance and quickly identify issues that emerge. Some of the process automation solutions provide multiple views and notifications that can help you stay ahead of bottlenecks, deadlines, and SLAs. You also need to look for no-code options that make it simple to build customized dashboards that prioritize the most important metrics front and center.
Process Excellence versus Operational Excellence
Process excellence is often confused with other related terms like operational excellence, or business excellence. It is therefore important to differentiate and define the differences between them.
Let us first define what operational excellence is. Operational excellence (OpEx) is a discipline that aims at improving all aspects of an organization’s operations, from the bottom up. OpEx initiatives achieve change by addressing internal issues about the company’s culture or technology and then building on those changes.
This discipline has a broader focus when compared to process excellence. The typical activities that are covered under operational excellence include-
- Building infrastructure for changes
- Developing the discipline for completing actions and processes consistently
- Shifting team focus from product quality to customer experience
- Prioritizing process effectiveness and agility of the business
- Deploying a system of engagement that bridges process gaps and data silos
- Achieving stack extensibility for leveraging the capabilities of apps and systems
Process excellence on the other hand is the practice of continually improving the efficiency, effectiveness, and quality of business processes and operations. The scope of process excellence is smaller than that of operational excellence. Operational excellence is about changing the culture, perceptions, and mindsets of everyone in the organization, while process excellence is focused on changing the process performance.
Process Excellence versus Business Excellence
Process excellence and business excellence are often considered to mean the same thing. If we observe closely, these two terms differ in their scope. Process excellence is essentially a framework for improving the efficiency and performance of business processes. The focus of process excellence initiatives is more on the process performance, than on the whole business.
Business excellence on the other hand is a comprehensive approach to improving business outcomes. It would be right to say that business excellence is a combination of process excellence and operational excellence. All the methodologies and systems that focus on improving overall business outcomes may be grouped under business excellence.
Top 10 Tools for Achieving Process Excellence
Process excellence is essentially a combination of all those methodologies and tools that help businesses achieve success. It can be considered a combination of art and science. A toolkit that combines various methodologies or systems that work together to achieve process excellence is considered a process excellence methodology. Let us consider the top 10 process excellence tools that can be used either as stand-alone methods or can be combined to achieve business success.
1. Six Sigma
This is a data-driven methodology that focuses mainly on reducing process variability and defects. The basis of this approach is a statistical analysis that helps identify the root cause of issues and implement corrective improvements. The Six Sigma methodology combines two project management frameworks – DMAIC (Define, Measure, Analyze, Improve, Control) for existing processes, and DMADV (Define, Measure, Analyze, Design, and Verify) for new processes.
2. Lean
Lean methodology mainly focuses on maximizing customer potential while minimizing waste. It focuses on creating more value with fewer resources by eliminating non-value-adding activities or processes. Continuous improvement, respect for people, standardized work, pull-based production, and just-in-time production are some of the popular lean methodologies.
3. Kaizen
Kaizen is a Japanese term that means continuous improvement. It involves small, incremental changes aimed at optimizing processes and eliminating waste. This methodology encourages employee involvement and teamwork, fostering a culture of continuous learning and improvement.
4. Total quality management
Total quality management (TQM) is a management approach to process improvement that aims at achieving long-term success through customer satisfaction. The primary focus of TQM is on continuous improvement, employee empowerment, and process efficiency. Core TQM principles lean towards customer centricity, management commitment, employee involvement, and continuous improvement.
5. Value stream mapping
This is a lean tool that represents the flow of materials and information within the process. Mapping a process through this methodology helps identify bottlenecks, wastages, and improvement opportunities. Based on the information provided by the value stream diagram, organizations can optimize their processes by focusing on value-adding activities and reducing non-value-adding activities.
6. Balanced Scorecard
This is a strategic process management tool that translates the vision and strategy of the organization into a set of performance measures. With the help of this tool, organizations can get a comprehensive view of their overall performance based on 4 perspectives – financial, customer, learning and growth, and internal processes.
7. 5S
This is a workplace organization methodology with its origins in Japan. It derives the name 5S from the 5 steps that make up the methodology. The 5S’s are – Sort-Set in order-Shine-Standardize-Sustain. The primary focus of the 5S methodology is to create a clean, organized, and efficient work environment that enables safety and productivity.
8. Plan-Do-Check-Act (PDCA)
This is a continuous improvement cycle that is used to solve problems and improve processes. The main components of this methodology are – planning the change (Plan), implementing the change (Do), reviewing the results (Check), and making necessary adjustments (Act). The PDCA cycle is repeated for continuous process improvement.
9. Business process reengineering
This is a process improvement methodology that involves a radical redesign of an organization’s processes for achieving significant performance improvements. Business process reengineering helps reduce process costs and improve the speed and quality of the product cycle. Success of business process reengineering requires a thorough analysis of existing processes and the development of new processes that are streamlined and more efficient.
10. Gemba Walk
This is a lean management methodology that involves managers and leaders visiting workplaces (gambas) to observe processes, engage with employees, and identify areas for improvement. These walks provide them with a better understanding of the work environment.
5 Best Practices in Process Excellence
1. Monitor the process constantly
The best way for companies to keep an eye on their processes is to visualize and track their progress. Look at the big picture while choosing management methodologies and tools.
For example, Six Sigma principles can help achieve the required results by delivering consistent, positive outcomes with minimum variation. As a business manager, when you break down each process into steps and analyze each one of them to identify potential loopholes.
Reviewing processes regularly helps in identifying and eliminating risks on time. Business process management platforms are meant to align the delivery of business goals through the organization, management, improvement, and automation of all types of processes.
There are several ways to monitor your processes, from time-tracking software to programs that monitor your budget and resources. You need to choose the right technology that lets you keep an eye on each step of the process. When you constantly evaluate and measure your requirements, you will know how much working capital you need at all times.
2. Keep it lean
According to Shigeo Shingo, an expert in manufacturing practices, “The most dangerous kind of waste is the waste we don’t recognize.” Process excellence is all about improving existing steps and tasks by planning, organizing, and preparing for long-term growth. When you know your business goals clearly, you can map out the best and easiest way to get there.
However, it is equally important to recognize what to avoid. By identifying ways to save money, resources, and time without compromising on the quality of your output, you can eliminate waste and keep your processes lean.
3. Keep processes agile
Quoting Tom Peters, “Excellent firms do not believe in excellence, only in constant improvement and change. Businesses need to be more innovative and productive if they want to stand out from the competition and scale up.
To achieve this, businesses need to stay on their toes and remain agile for survival and long-term growth. Remaining agile in your operations helps you keep up with the latest trends in the industry and identify which processes you need to change or upgrade to build a business model that evolves with the times.
4. Maintain customer centricity
To stay in business, you need to keep your customers happy! Customers are the key ingredients to consistent business growth. While planning processes you must always do so with customer expectations in mind.
Invest in time and resources that are needed to understand the target audience and their pain points, and evaluate if the touch points are up to these expectations. Once you understand the target audience fully, you are in a better position to provide personalized experiences and exceptional targeted services. Process excellence is at its best when it focuses on customer-centricity at all times.
5. Keep the company culture alive
According to Henry Ford, “Coming together is a beginning, keeping together is progress, and working together is success.” To achieve success in process excellence, it is important to create a culture of process excellence that starts from the top and makes its way down to the employees.
When the C-suite emphasizes the importance of continuously working on its processes, they lead by example. An “all deck hands” approach when working towards process excellence is required when the organization is working towards success.
Involve and empower each one of your employees and team members while incorporating changes for achieving process excellence, so that they are equally invested in the outcomes. When creating your processes, walk in your employee’s shoes to understand their obstacles and find practical solutions.
Workflow Automation and Process Excellence
As mentioned in the best practices in process excellence, adopting technology to improve process outcomes is one of the most effective ways of implementing process excellence initiatives. Workflow automation is an effective way of improving process outcomes. A no-code workflow automation software like Cflow makes your process excellence initiatives more effective and successful.
Cflow keeps expanding its feature offerings to improve customer experiences. One such feature is the Agile-Kanban feature which improves the prioritization of tasks. You can acquire a simplified framework for visualizing multiple tasks with Kanban in Cflow. There are several other features that Cflow has to offer that can make your process excellence efforts a huge success.
Conclusion
Process excellence initiatives help businesses achieve high productivity, growth, sustainability, and profitability. Process excellence is key to delivering quality business outcomes, and setting up excellent, effective, and efficient processes. Investing in a no-code workflow automation solution like Cflow boosts process excellence initiatives. Make Cflow a part of your process excellence efforts.
Sign up for the free trial now.