AI-Driven Automation in Manufacturing Workflows: Smarter Processes for Modern Factories
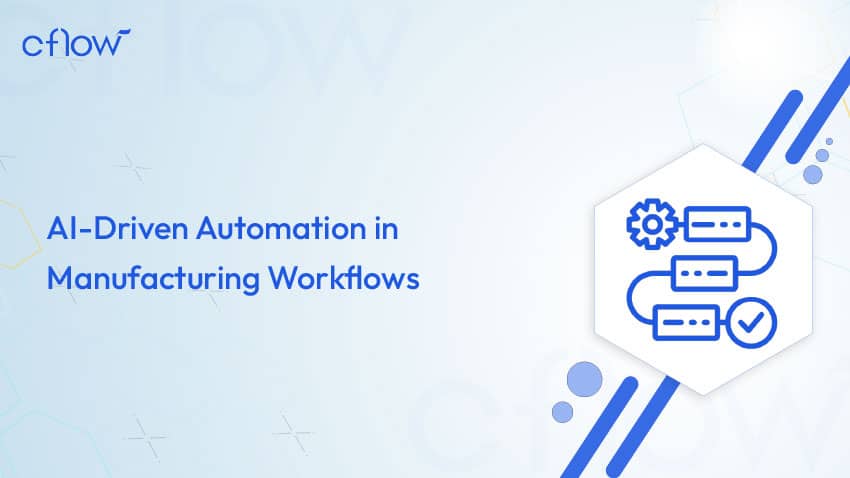
Key takeaways
- AI-powered workflow automation transforms manufacturing by enabling predictive maintenance, real-time quality control, and autonomous inventory management.
- Cflow empowers non-technical teams to automate complex factory workflows using a drag-and-drop builder, OCR, escalations, and mobile-ready forms.
- Manufacturers reduce downtime, avoid stockouts, and speed up approvals with intelligent workflows that adapt to real-time shop floor data.
- With Cflow, UK manufacturers move beyond spreadsheets and silos to embrace lean, self-correcting, and scalable automation solutions.
Welcome to the Machine Renaissance
Factories no longer hum—they think.
Walk into a modern manufacturing floor, and the rhythmic clank of steel does not just greet you. There’s something else in the air: precision. Data. Decisions are being made on the fly, not by managers, but by algorithms trained to see patterns no human eye can catch.
Welcome to AI-driven workflow automation, where workflows aren’t just automated—they’re aware.
This isn’t just about speeding up a production line. It’s about eliminating waste before it’s made. It’s about self-correcting systems, predictive maintenance, and supply chains that reorder before stock-outs strike.
It’s lean—but with a brain.
Why Now? Because “Efficiency” Just Got Smarter
The pandemic cracked open vulnerabilities in manufacturing that had been duct-taped for years: paper-based approvals, delayed decisions, and siloed systems. The fix? Not more people. Not more hardware.
The fix is intelligent workflow automation, and AI is its pulse.
Think:
- Workflows that learn.
- Machines that predict.
- Systems that act without waiting for someone to click “approve.”
In the UK’s push toward smart factories and digital transformation, AI isn’t the future. It’s the blueprint.
And Then There’s Cflow
Let’s not tiptoe around it: most manufacturers still wrestle with spreadsheets, email threads, and approval chains longer than a warehouse aisle.
Cflow is the no-code, AI-powered solution for those who are done wrestling.
- Visual drag-and-drop workflows.
- OCR that eats paper forms for breakfast.
- Triggers, escalations, and dynamic roles—all without touching a line of code.
This is automation you control. And when paired with AI? That’s a factory floor that adapts in real time.
The Tangible Benefits of AI in Manufacturing Workflows
Not every buzzword pays rent.
AI does—every single shift.
It’s not just about looking futuristic on a slide deck. AI-powered workflow automation delivers real, repeatable gains right on the factory floor.
Let’s break it down.
1. Downtime Becomes History
In traditional setups, machines break, and then someone scrambles. That’s a costly game of chance.
With AI-enabled predictive maintenance, your workflows act the moment sensors detect anomalies: unusual vibrations, overheating, or run-time thresholds crossed.
Cflow connects these data points through condition-based triggers. Once those thresholds are breached, the system:
- Initiates a maintenance request automatically
- Routes it to the right team based on machine type or urgency
- Escalates if there’s no action within a defined window
This isn’t just automation—it’s foresight built into your process.
The impact?
- Drastically reduced unplanned downtime
- Maximised machine uptime
- Less firefighting, more forward planning
Even better, your maintenance manager gets to sleep through the night.
2. Quality Control Gets a Sixth Sense
Random sampling belongs in the 90s.
AI takes your quality process from guesswork to real-time precision.
Cflow workflows tap into inspection data and forms, using OCR to validate readings, compare against thresholds, and flag non-compliance instantly.
When a deviation is detected:
- The defective unit is quarantined automatically
- A workflow triggers an alert to QA with all supporting documents/images
- Escalation rules kick in if it’s not handled within the SLA
And every action is logged, creating a paperless trail for compliance, audits, and future analysis.
You don’t just catch defects. You learn from them in real-time.
3. Approvals: Stop Holding Everything Hostage
Ever had production stall because someone forgot to approve a PO or repair ticket?
Cflow fixes that.
AI-driven workflows identify who needs to act, how long they’ve delayed, and what happens if they don’t.
Approvals are sent:
- Via email with actionable “Approve/Reject” buttons
- Through Slack or Teams
- Straight to mobile as push notifications
Best part? No login required.
You could be in a meeting, at lunch, or 30,000 feet in the air—approvals still happen.
That’s no bottlenecks, no chasing, and no downtime because someone forgot to open an email.
4. Inventory Replenishment Becomes Autonomous
Stock-outs and overstocking kill margins.
Manual reorder processes? Too slow and too error-prone.
Cflow’s AI logic monitors real-time inventory levels. When stock falls below defined thresholds:
- It checks vendor schedules and lead times
- Calculates reorder quantities based on historic usage
- Triggers purchase requests and notifies procurement
No human needed. No delay.
The workflow can even prioritise vendors based on cost, delivery speed, or contract terms.
It’s like giving your supply chain team an extra pair of eyes—and a predictive brain.
Use Cases: Where the Magic Actually Happens
These aren’t hypotheticals—they’re how manufacturers are using AI and Cflow to turn chaos into clarity.
️ Use Case 1: Machine Maintenance Logs with OCR + Webhooks
Let’s say a line operator finishes a shift and scrawls down readings and error codes on a paper log.
Normally, this sits in a dusty binder or gets passed manually to a supervisor, who might process it days later. Not anymore.
With Cflow, that log is scanned and instantly processed using OCR (Optical Character Recognition). The system extracts key values: machine ID, runtime, fault codes, and timestamps. It then checks the values against pre-set thresholds. If it detects abnormal patterns—say, a runtime spike or frequent errors—it kicks off a maintenance approval workflow on the spot.
If that workflow isn’t approved within, say, 2 hours?
Time-based escalations fire. A webhook then notifies the maintenance dashboard and sends a Slack alert to the shift supervisor.
The result:
- Maintenance requests are proactive, not reactive
- Nothing gets missed or delayed
- Audit trails are airtight
You’ve just eliminated clipboard clutter and built a smarter maintenance culture.
Use Case 2: Defect Routing in the Production Line
A defect shows up mid-shift—a bent part, a faulty weld, a misaligned sensor. Usually, the operator has to log it manually, notify QA, and wait for someone to investigate.
With Cflow, the process is immediate and automated. The operator submits a defect report via a public form—no login required. The form captures images, batch numbers, defect type, and urgency. Based on conditional logic, the workflow auto-routes the request:
- Low-priority? It goes to the QA team for review.
- Critical fault? It jumps straight to Engineering and Plant Ops.
What if no one responds within the SLA window?
Cflow’s email escalation triggers nudge the next approver. If still no action, it escalates up the chain to the plant manager.
All related documents—repair guides, testing protocols, compliance checklists—are automatically attached within the workflow.
Result?
- Real-time traceability
- Zero hand-offs lost in translation
- Actionable defect data logged for analytics
In short, defects get fixed before they cost you production time.
Use Case 3: Supplier Quote Approval on Mobile
Your procurement team is evaluating three new vendors for CNC parts. One of them sends a quote via email during a trade show. Typically, this would get buried or delayed waiting for an office review.
Instead, with Cflow, the procurement officer enters the quote data into a mobile-friendly workflow form on their tablet. The system instantly compares the new quote against historical vendor pricing using AI-based validation rules. Any major deviation? It flags the quote and adds a comment.
The department head receives an email approval request with the quote details and embedded “Approve” and “Reject” buttons—no login needed.
Even if they’re out of office, they can approve it from their phone.
Boom—decision made during a coffee break.
The entire quote approval is logged, time-stamped, and stored for compliance. No paper trail. No bottlenecks. Just procurement velocity.
End-to-end workflow automation
Build fully-customizable, no code process workflows in a jiffy.
What Makes Cflow a Power Move for Manufacturing Teams
Here’s the hard truth most vendors won’t tell you:
Most workflow tools are built for HR teams or marketing agencies, not the unforgiving pace of a manufacturing floor.
Cflow? It’s forged for industry. It thrives in environments where seconds matter, approvals can’t wait, and compliance is non-negotiable. Here’s how it punches above its weight:
Drag-and-Drop Workflow Builder
Think of it as LEGO for process design—but smarter.
With Cflow’s visual workflow builder, plant teams can map out complex processes like “If machine runtime > 12 hours → trigger inspection → notify maintenance lead → escalate after 30 mins delay” in just a few clicks.
No devs. No code. No waiting on IT.
Whether it’s automating inventory replenishment or routing production logs, the logic is clean, visual, and entirely under your control.
This isn’t a toolkit—it’s a command centre.
AI-Lite Logic Without the Jargon
You don’t need a data science degree to think like an algorithm.
Cflow brings just enough AI muscle, wrapped in plain English.
Set workflows to change visibility based on conditions.
Make fields required only when specific criteria are met.
Use fuzzy search to pull up machine records even if the ID is partially entered.
Enable escalations so that missed approvals don’t stall production.
It’s intelligence with just the right dose of automation—designed for people who build things, not write code.
Real-Time Dashboards and Workflow Monitors
Data isn’t useful if it hides in silos.
Cflow turns your workflows into live dashboards that track what matters:
- Maintenance backlogs
- Pending approvals
- Defect rates
- SLA breaches
Need proof for an audit? Export everything—PDF, Excel, CSV.
Need deeper analytics? Push the data into Power BI and slice it your way.
This isn’t analytics for analytics’ sake. It’s visibility that drives real-time action.
Factory-Ready Mobility
Cflow understands that supervisors aren’t tethered to desks—they’re walking the floor.
With native mobile apps for Android and ios, your team can:
- Submit defect reports with photos
- Approve supplier quotes from anywhere
- Check pending maintenance logs
- Trigger new workflows—on the go
No more waiting for someone to “get back to their system.”
With Cflow, your system is wherever you are.
Closing Shot: It’s Not Just Automation—It’s Elevation
AI-driven automation isn’t about replacing workers. It’s about replacing inefficiencies.
And in the UK’s evolving industrial landscape, companies that adopt Cflow aren’t just saving time—they’re creating smarter factories that think, act, and grow on their own terms.
So go ahead. Ditch the spreadsheet. Ditch the chaos. Embrace intelligent automation that knows its job—so your team can do theirs better.
Conclusion: UK Manufacturing Needs Smarter Workflows—Now
Britain’s manufacturing sector is evolving fast, and those still clinging to email chains and legacy systems? They’re not just behind—they’re invisible.
With AI-driven automation, every approval, alert, and exception is logged, tracked, and optimised.
With Cflow, that evolution doesn’t take months. It takes minutes.
Whether you’re in Sheffield, Birmingham, or the outskirts of Aberdeen, factory floors across the UK can gain from one thing: clarity.
Clarity in approvals. Clarity in quality control. Clarity in operations.
So, here’s your move:
Modernise. Mobilize. And make your workflows smarter with Cflow.
FAQ
1. How does AI-powered workflow automation improve manufacturing efficiency?
AI-powered workflow automation enables real-time data analysis, predictive maintenance, and dynamic approvals. This reduces downtime, prevents stockouts, eliminates manual errors, and ensures faster decision-making—all of which enhance overall factory efficiency.
2. What types of manufacturing workflows can be automated with Cflow?
Cflow can automate a wide range of workflows, including maintenance requests, defect reporting, supplier quote approvals, inventory replenishment, quality assurance processes, and production scheduling—without writing a single line of code.
3. Can Cflow integrate with existing factory systems and sensors?
Yes. Cflow supports webhooks and API integrations, allowing it to connect with ERP systems, IoT sensors, and production monitoring tools. This ensures that real-time data flows seamlessly into automated workflows for better decision-making.
4. Is Cflow suitable for non-technical teams on the factory floor?
Absolutely. Cflow is built for usability. Its visual workflow builder, no-code setup, mobile access, and intuitive dashboards make it easy for shop floor teams, supervisors, and managers to automate and monitor processes without technical expertise.
Automate your workflows with our Cflow experts.What would you like to do next?
Get your workflows automated for FREE