AI automation for logistics and shipping workflows
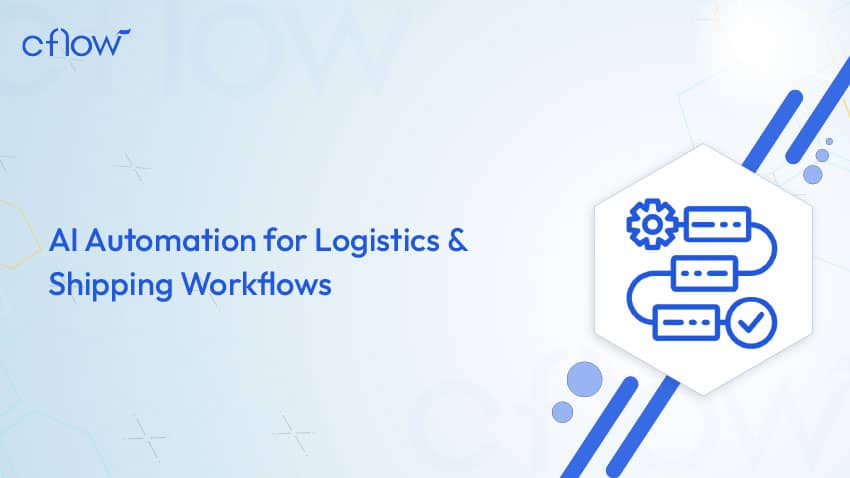
Key takeaways
- AI automation eliminates bottlenecks in logistics by optimising routing, load balancing, and real-time shipment tracking.
- AI-powered shipping workflows improve last-mile delivery speed, carrier selection, and exception handling.
- Companies using AI in logistics report lower fuel costs, reduced delays, and improved customer satisfaction.
- Platforms like Cflow enable no-code AI-powered workflows, making automation accessible without deep IT dependency.
The AI in logistics market is projected to grow from $18.01 billion in 2024 to $26.34 billion in 2025, reflecting a compound annual growth rate (CAGR) of 46.2%.
From fluctuating fuel prices to global supply chain disruptions, inefficiencies in shipping workflows can quickly snowball into higher costs and missed SLAs. Traditional automation falls short when real-time adaptation is needed. This is where AI automation for logistics and shipping workflows comes into play.
AI doesn’t just automate tasks — it makes decisions, predicts outcomes, and continuously improves workflows. Whether it’s route optimisation, smart freight allocation, or real-time exception management, AI-driven workflows are redefining how modern logistics operates.
This blog explores how businesses can integrate AI into their logistics and shipping workflows to streamline operations, cut costs, and improve delivery performance.
What is AI Automation in Logistics and Shipping?
AI automation refers to embedding artificial intelligence capabilities into operational workflows to carry out repetitive logistics and shipping tasks with minimal human input. Unlike traditional rule-based automation, AI continuously learns from data and adapts based on real-time variables like traffic conditions, delivery volumes, or customs delays.
For instance, an AI system can:
- Analyse route patterns and dynamically adjust deliveries based on weather or traffic.
- Automate carrier selection based on price, reliability, and service performance.
- Trigger real-time alerts for delayed or failed shipments and suggest recovery options.
This proactive, self-learning approach minimises disruptions, shortens delivery cycles, and enhances customer experience.
Why AI Is Critical for Modern Logistics Operations
Logistics is no longer a back-office function—it is a strategic capability that directly impacts profitability, brand reputation, and customer loyalty. Yet, many logistics workflows remain static, reliant on outdated rules-based systems or manual processes that cannot respond to fast-changing conditions. AI introduces adaptability, speed, and intelligence that traditional automation lacks.
Volatility in Demand and Fuel Prices
Fluctuations in customer demand and fuel prices strain logistics planning. Static workflows are ill-equipped to respond to rapid changes. AI enables intelligent resource reallocation by analysing historical data, weather forecasts, geopolitical developments, and consumer behaviour in real time. This allows logistics teams to rebalance fleets, adjust delivery windows, and avoid financial shocks from inefficient routing or under-utilised assets.
Last-Mile Delivery Complexity
A report by DS Smith revealed that 84% of e-commerce businesses across the UK and Europe experienced last-mile delivery cost increases, with 39% seeing rises of more than 10% in 2024.
The last mile accounts for over 53% of total shipping costs (Capgemini Research Institute), yet it remains the most unpredictable. AI simplifies last-mile complexity by dynamically recalculating routes, optimising drop-off sequences, and factoring in real-time events like road closures or customer availability. It ensures more deliveries are completed on the first attempt—reducing failed deliveries and associated costs.
Rising Customer Expectations
Today’s customers expect not just timely deliveries but live updates, accurate ETAs, and full visibility into their order’s journey. Without intelligent systems, businesses struggle to meet these expectations. AI enhances customer experience by providing real-time shipment tracking, delay predictions, and proactive notifications—turning logistics into a competitive advantage.
Manual Intervention in Shipment Tracking
Relying on manual input or rigid rule-based systems delays responses to shipment issues. AI automates tracking across multiple carriers and warehouse systems, instantly identifying anomalies such as delays, misroutes, or damages. It can even trigger corrective actions or alert stakeholders without human intervention, ensuring continuity and accountability.
AI addresses these gaps with predictive intelligence, adaptive learning, and real-time decision-making, making logistics operations more resilient, scalable, and customer-centric.
Who Should Invest in AI Automation for Logistics?
The UK has witnessed significant growth in the AI sector, with the number of AI-focused companies expanding by 600% over the past decade.
AI workflow automation is no longer a luxury reserved for large logistics enterprises. Decision-makers across business sizes and sectors are turning to AI to drive efficiency, scalability, and profitability. If you fit into one of these categories, it’s time to take action:
Logistics Managers: Automate shipment planning, reduce fuel usage, and improve fulfilment timelines across regions.
Supply Chain Directors: Gain cross-functional visibility, optimise vendor coordination, and future-proof operations with adaptive decision-making.
3PL Providers: Offer AI-enabled workflows to clients as a competitive differentiator, reduce brokerage errors, and increase operational capacity.
E-commerce Fulfilment Teams: Manage peak season volumes with confidence, automate reverse logistics, and increase delivery reliability.
Digital Transformation Leaders: Integrate AI workflows as part of a broader tech strategy to improve operational agility, reduce risk, and optimise ROI.
Whether your focus is delivery performance, cost savings, or customer experience, AI workflow automation provides a strategic advantage—especially when implemented through flexible no-code platforms like Cflow.
Key Logistics and Shipping Workflows Enhanced by AI
AI is not a blanket solution—it delivers the most value when applied to specific high-impact logistics functions. Below are the core workflows where AI can significantly elevate operational efficiency and decision-making.
1. Smart Route Optimisation
AI-powered route optimisation combines GPS data, traffic feeds, weather inputs, and fleet constraints to recommend the fastest and most cost-efficient delivery paths. UK-based carrier DPD uses similar AI routing to reduce fuel consumption and improve first-time delivery success. Real-time recalculation ensures that routes adapt on the fly, reducing miles driven, idle time, and emissions.
2. Dynamic Carrier Selection
Choosing the right carrier can impact delivery speed, cost, and reliability. Instead of relying on static rate cards, AI algorithms assess performance data, capacity, and service levels in real time to assign each shipment to the most suitable carrier. This ensures optimal resource utilisation and stronger delivery KPIs, particularly for companies managing multiple regional or global partners.
3. Automated Freight Matching
AI enhances freight matching by analysing shipment dimensions, weight, priority level, and delivery timelines. It then pairs the shipment with the most suitable vehicle or carrier slot. This reduces empty miles, improves vehicle fill rates, and boosts overall fleet productivity. For 3PLs and freight brokers, this automation can eliminate hours of manual coordination and improve margin per load.
4. Predictive Inventory Replenishment
AI integrates with inventory management systems to forecast stock needs by analysing consumption patterns, seasonal spikes, and promotional cycles. Retailers like Tesco use similar algorithms to prevent overstocking or stockouts. For distribution hubs, this means more efficient pallet loading, fewer returns, and better service continuity even during demand surges.
5. Real-Time Exception Management
Delays, damages, and route disruptions are inevitable—but response times make all the difference. AI-enabled workflows constantly monitor shipments and detect exceptions like temperature breaches (in cold chains), traffic hold-ups, or missed pickups. When issues occur, AI can automatically reroute shipments, alert drivers, or initiate customer notifications—minimising escalation and improving SLA adherence.
Benefits of AI-Driven Workflow Automation in Logistics
AI does more than speed things up. It makes operations smarter, more efficient, and aligned with business outcomes. These are the most tangible benefits realised by logistics teams implementing AI workflows.
1. Reduced Operational Costs
AI minimises fuel costs, warehousing expenses, and overtime labour by reducing delivery windows, increasing load efficiency, and automating repetitive workflows. According to McKinsey, logistics firms using AI for route and load optimisation saw cost reductions of up to 15% across operations.
2. Improved Delivery Accuracy
Intelligent route planning, inventory checks, and automated dispatch scheduling mean fewer misroutes, missed deliveries, or shipment errors. Accuracy leads directly to lower re-delivery costs and better customer satisfaction.
3. Greater Visibility
AI centralises data from disparate systems—carriers, warehouses, ERP tools—into unified dashboards that provide logistics managers with a real-time snapshot of operations. This level of visibility aids compliance, traceability, and strategic planning.
4. Faster Turnaround Times
Manual processes such as documentation approval, dispatch scheduling, and delivery confirmations are replaced with real-time triggers and automated approvals. This results in quicker order cycles and faster response to customer requests.
5. Better Customer Experience
AI enhances CX by offering proactive shipment updates, real-time delay alerts, and resolution workflows that keep customers informed. It also powers chatbots and self-service portals for faster communication across the delivery journey.
Case Studies: AI in Action
To illustrate how AI workflow automation delivers results, here are two real-world examples from the UK logistics sector. These companies have leveraged AI not as a buzzword, but as a practical tool to improve efficiency, reduce costs, and meet customer demands.
Ocado’s Smart Warehouse Strategy
Ocado, the UK-based online supermarket and logistics technology provider, has implemented advanced AI-driven automation across its fulfilment centres. The company uses intelligent warehouse robotics powered by real-time data to manage inventory, pick products, and schedule shipments. AI systems continually optimise packing routes and stock placement to reduce pick times and human error. In a 2024 update by The Guardian, Ocado confirmed that integrating AI across its facilities helped reduce logistics costs and improve throughput, enabling faster grocery deliveries even during peak demand periods.
Royal Mail’s AI Sorting Efficiency
Royal Mail has invested significantly in AI-based automation to modernise its parcel sorting and last-mile delivery operations. Using machine vision and AI-driven logistics workflows, the company has streamlined the way parcels are identified, categorised, and routed. According to a 2024 report by the Financial Times, Royal Mail’s deployment of automated sorting machines and intelligent delivery algorithms has improved speed, reduced sorting errors, and boosted customer satisfaction across the UK. These investments have been part of the organisation’s wider effort to compete with agile e-commerce carriers by reducing human bottlenecks in fulfilment.
Challenges and Considerations
AI automation delivers powerful advantages, but businesses must address a few critical hurdles to ensure successful implementation and ROI.
Integration with Legacy Systems
Many logistics firms still rely on outdated ERPs and tracking tools that don’t easily connect with modern AI platforms. Choosing solutions with open APIs, low-code integration, and early tech partner support can minimise disruption and speed up deployment.
Data Quality and Management
AI outcomes depend entirely on the quality of data it receives. Inconsistent or siloed information leads to inaccurate predictions. Centralising data, cleansing legacy records, and enforcing governance policies are essential to building trust in AI-driven decisions.
Change Management
AI can trigger resistance if teams fear losing control or relevance. Clear communication, upskilling programs, and involving users early in the automation rollout are vital. UK research shows transformation success rates triple when change management is prioritised from day one.
Cflow: No-Code AI Workflow Automation for Logistics Teams
Cflow enables logistics and supply chain teams to build, test, and deploy AI-powered workflows without writing code. It’s no-code interface empowers operations managers to digitise processes rapidly while maintaining full control and flexibility.
Smart Freight Dispatch: Create workflows that automate approvals for freight dispatch, carrier assignment, and delivery documentation in a centralised system.
Adaptive Routing Rules: Define intelligent routing logic based on delivery type, destination, or carrier performance, so the system always selects the most optimal path.
Real-Time Tracking Integration: Seamlessly connect to GPS, TMS, or API-based shipment tracking tools. Trigger alerts and update customers automatically as shipments progress.
Bottleneck Visibility: Cflow’s analytics dashboard helps identify slow approvals, routing errors, or resource constraints in real time—so you can fix issues before they escalate.
Team Collaboration: Assign tasks, approvals, or exceptions dynamically to internal teams or 3PL partners based on workload, priority, or location.
Conclusion
With Cflow, even small or mid-sized logistics teams can implement enterprise-grade AI workflows without requiring a dedicated IT team—making transformation accessible and scalable.
As customer expectations rise and shipping logistics become more complex, businesses can’t afford to rely on outdated, manual processes. From dynamic routing to real-time tracking, AI-powered workflows transform logistics from reactive to proactive.
Platforms like Cflow make it easy to build and deploy intelligent logistics workflows without writing code. Whether you’re a logistics provider or an enterprise with global shipments, AI automation will help you move faster, respond smarter, and grow stronger.
Start your free trial of Cflow today and streamline your logistics workflows with the power of AI.
FAQs
1. What is the future of AI in logistics?
AI will enable fully autonomous logistics operations by enhancing real-time decision-making, predictive analytics, and cross-platform integration—improving resilience and agility.
2. How do you integrate AI into a workflow?
Integration involves mapping existing processes, identifying automation gaps, and using platforms like Cflow that support low-code APIs and seamless system connectivity.
3. What are the problems with AI in logistics?
Challenges include data silos, integration with legacy systems, lack of skilled personnel, and employee resistance—all of which require proactive change management.
4. How is AI used in reverse logistics?
AI optimises returns by automating item inspections, tracking reverse shipments, and predicting resale or refurbishment routes, reducing waste and turnaround time.
5. What is an example of workflow automation?
Automated route planning is a great example—AI dynamically selects the best delivery paths based on real-time traffic, weather, and package priority.