Production Part Approval Process (PPAP): Everything You Need to Know
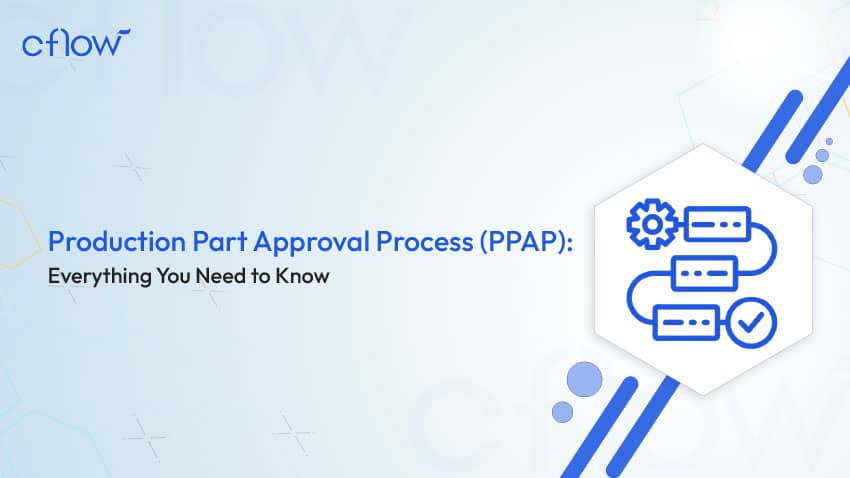
Key takeaways
- The Production Part Approval Process (PPAP) is essential for verifying supplier components meet customer specifications before mass production.
- PPAP ensures quality consistency, reduces defects, and maintains traceability in industries like automotive and aerospace.
- Companies implementing PPAP improve supplier relationships, prevent costly recalls, and meet IATF 16949 compliance.
- Automating PPAP workflows enhances accuracy, reduces delays, and streamlines multi-stakeholder approval processes.
In industries where product reliability is non-negotiable—such as automotive, aerospace, and heavy machinery—ensuring each part meets exacting standards is vital. One defective part can compromise an entire assembly, disrupt production, or lead to costly recalls. This is where the Production Part Approval Process (PPAP) becomes indispensable.
PPAP is not just a documentation procedure; it is a framework that fosters supplier transparency, standardisation, and product conformity. Originally developed by the Automotive Industry Action Group (AIAG), PPAP has become a global standard for part approval in any complex manufacturing ecosystem.
Understanding how PPAP works—and how to optimise it—is critical for manufacturers, quality engineers, and supply chain professionals who aim to meet customer requirements while controlling costs and maintaining process efficiency.
In this blog, what we are going to discuss is a comprehensive view of PPAP—from its meaning and stages to benefits, challenges, and tools for automation.
What is the Production Part Approval Process (PPAP)?
The Production Part Approval Process (PPAP) is a standardised process in the manufacturing industry that validates a supplier’s ability to consistently produce parts that meet customer design and quality requirements. It serves as a mutual agreement between the customer and the supplier that the production process is capable and the parts produced will meet expectations in terms of quality, performance, and consistency.
This process is essential when launching new products or making changes to existing designs or processes, as it provides documented evidence that both the product and its associated manufacturing process are fully understood and controlled. PPAP plays a critical role in preventing defects, ensuring compliance with industry standards, and maintaining traceability throughout the production lifecycle.
Cloud-based PPAP systems can reduce total approval timelines by up to 50%, significantly accelerating product launches.
PPAP consists of 18 elements or documents, each serving to confirm different aspects of design validation, process capability, and product conformity. These documents are submitted to the customer, who reviews and approves them before full-scale production begins.
Key Objectives of PPAP:
- Ensure the design and specification requirements are clearly understood.
- Validate that the manufacturing process is capable of consistently producing the part.
- Establish a formal approval between the supplier and the customer before full-scale production.
Example Scenario:
An automotive Tier 2 supplier manufacturing seat belt retractors must undergo PPAP approval before their parts are used in a new vehicle model. This ensures that every seatbelt meets safety standards and performs reliably across production runs. Without a PPAP-approved process, any defect in the retractors could lead to massive safety risks and regulatory consequences, not to mention vehicle recalls and loss of customer trust.
Evolution of PPAP and Its Cross-Industry Adoption
The Production Part Approval Process (PPAP) was originally developed by the Automotive Industry Action Group (AIAG) in the 1990s to tackle rising quality issues and ensure uniform supplier processes across the auto industry. As supply chains globalized and customer demands grew more complex, PPAP became a critical component of supplier quality assurance.
Over time, industries beyond automotive—such as aerospace, medical devices, and heavy equipment manufacturing—adopted PPAP or adapted it to their own quality systems. Today, PPAP is not just a compliance requirement; it’s a benchmark for supplier readiness and process stability in any precision manufacturing environment.
When is PPAP Required?
PPAP is typically required:
- When introducing a new part or product: To validate that the supplier can meet all design and quality expectations from the start of production.
- After a design or process change: If there’s a change in material, design specifications, tooling, equipment, or manufacturing method, PPAP ensures that the change doesn’t negatively affect the part.
- When using a new or alternate supplier: Even if the part design remains the same, a new supplier must undergo PPAP to confirm capability and consistency.
- After moving production to a new facility: Changing the production location can introduce variability; PPAP confirms that the same quality standards are upheld.
- When resuming production after being inactive for 12+ months: A dormant process needs revalidation to ensure that tooling, equipment, and procedures still produce parts to specification.
These triggers are critical checkpoints where quality and process stability must be reassessed. Most OEMs or Tier 1 suppliers will request a PPAP submission at these points to verify conformance and mitigate risk, especially in safety-critical components where failure is not an option.
Levels of PPAP Submission
PPAP is divided into five submission levels, each indicating the depth of documentation required:
- Level 1 – PSW Only: This level includes only the Part Submission Warrant (PSW). It is typically used when there is minimal risk involved, such as cosmetic parts or non-critical components.
- Level 2 – PSW with Limited Supporting Data: This includes the PSW plus selected documentation such as dimensional results or material certifications. It is often used for low-volume or legacy parts.
- Level 3 – PSW with Complete Supporting Data: This is the most common level of submission. It includes the PSW and all 18 required PPAP elements. This level ensures comprehensive review and approval, and is usually mandated for safety-critical parts.
- Level 4 – Customer-Defined Requirements: The customer specifies the exact documentation required. This level provides flexibility based on specific project or industry needs.
- Level 5 – PSW and Full Documentation with On-Site Review: All PPAP documentation is prepared and retained for an on-site evaluation by the customer. This is the most rigorous level and is used for high-risk or highly regulated parts.
Cross-Functional Roles Involved in PPAP
Effective execution of the PPAP process involves collaboration between multiple departments and stakeholders:
Supplier Quality Engineers (SQEs): Lead PPAP submissions and validate supplier capability.
Design Engineers: Provide and review design records and DFMEAs.
Process Engineers: Develop PFMEAs and control plans for production processes.
Procurement Teams: Communicate requirements to suppliers and ensure compliance during onboarding.
Regulatory/Compliance Officers: Review PPAP documentation for audit readiness and legal conformity.
Establishing cross-functional accountability ensures PPAP isn’t siloed, but instead, integrated across the organisation’s quality ecosystem.
18 Elements of a Complete PPAP
Each PPAP submission must contain a combination of the following 18 elements, depending on the level of submission and customer requirements:
- Design Records – Detailed drawings and specifications that define the part design. These are often customer-approved documents.
- Authorised Engineering Change Documents – Any engineering changes that are not included in the original design record but are authorised and approved.
- Customer Engineering Approval – Formal customer approval of parts obtained through prototype builds, testing, or specific evaluations.
- Design FMEA (DFMEA) – A proactive analysis of potential design failures and their effects on system performance.
- Process Flow Diagram – A graphical representation showing each step of the manufacturing process, from raw material to finished part.
- Process FMEA (PFMEA) – Identifies potential process failures and their impact on product quality, with mitigation actions defined.
- Control Plan – Outlines controls and inspection methods used at each process step to ensure consistent quality.
- Measurement System Analysis (MSA) – Evaluates the accuracy and precision of the measurement tools and systems.
- Dimensional Results – A report of actual measurement data for all product dimensions listed on the design record.
- Records of Material / Performance Tests – Documentation of test results that confirm material and product performance specifications are met.
- Initial Process Studies (SPC) – Statistical evidence showing that key process parameters are under control and capable.
- Qualified Laboratory Documentation – Certificates and accreditations of the labs conducting material or performance tests.
- Appearance Approval Report (AAR) – Confirms that parts meet visual and cosmetic requirements, often required for customer-facing components.
- Sample Production Parts – Actual physical parts submitted along with the PPAP package for evaluation.
- Master Sample – A signed and retained sample representing the standard for future production.
- Checking Aids – Any fixtures, gages, or tools used to inspect parts must be documented with calibration records.
- Customer-Specific Requirements – Any additional requirements outlined by the customer, varying by industry or project.
- Part Submission Warrant (PSW) – A summary document that certifies the part meets all customer requirements and includes sign-offs.
These documents collectively ensure traceability, compliance, risk mitigation, and consistent quality control across the entire supply chain. They also provide confidence to the customer that the supplier’s process is stable and capable of producing conforming parts over time.
Use Cases of Production Part Approval Process (PPAP)
The Production Part Approval Process (PPAP) is a vital quality assurance tool in manufacturing, particularly in the automotive, aerospace, and industrial sectors. It is used to verify that a supplier’s production process consistently yields parts that meet all customer specifications.
1. Automotive Component Manufacturing
One of the most common use cases of PPAP is in automotive manufacturing. Tier 1 and Tier 2 suppliers use PPAP to validate the quality and reliability of components like brake pads, fuel injectors, or steering columns before full-scale production. This ensures safety-critical parts are tested, documented, and traceable.
2. Aerospace Parts Validation
Aerospace OEMs require PPAP-like processes to ensure precision and compliance in parts such as turbine blades or structural assemblies. With the need for zero-defect tolerance, PPAP documentation supports FAA and EASA certification requirements.
3. Supplier Onboarding and Qualification
When onboarding a new supplier, companies use PPAP to assess the supplier’s production capabilities. It allows quality teams to evaluate whether the manufacturer can meet tolerance, design, and process control expectations before awarding bulk orders.
4. Engineering Change Management
If a product design changes—such as material substitution or a tooling update—a revised PPAP submission is often required. This ensures the change does not impact form, fit, or function, helping avoid production delays or quality issues.
5. Launching New Product Lines
PPAP is critical during new product introductions (NPIs). It provides structured validation that new parts meet all customer requirements before they are released to production, minimising rework or recalls after launch.
6. Requalifying After Production Downtime
If production has been paused for an extended period or if equipment has been relocated or significantly altered, manufacturers may perform a PPAP requalification to confirm that part quality remains consistent.
7. Quality Audits and Compliance
Manufacturers use PPAP documentation during audits to demonstrate that their production processes are well-controlled and compliant with standards such as IATF 16949. It serves as proof of due diligence in supplier quality assurance.
Customising PPAP for Specific Industries
While PPAP has automotive roots, other sectors adapt its principles to align with their regulatory and performance expectations:
Aerospace: PPAP is adapted to meet AS9145 and AS9102 standards, with even more rigorous documentation for flight-critical components.
Medical Devices: Modified to align with ISO 13485 and FDA 21 CFR Part 820, focusing on validation, traceability, and supplier qualification.
Heavy Equipment Manufacturing: Often combines PPAP with APQP (Advanced Product Quality Planning) to ensure robustness in new model development.
This adaptability ensures PPAP remains relevant across a wide array of industries focused on precision, safety, and compliance.
Benefits of Implementing PPAP
Implementing PPAP offers manufacturers and suppliers a structured framework to ensure production readiness and compliance. Beyond just fulfilling customer requirements, it provides strategic advantages in quality control, risk mitigation, and audit preparation.
1. Risk Mitigation
PPAP helps detect design or manufacturing issues early in the supply chain, preventing costly production errors, quality rejections, and safety issues down the line.
2. Compliance with Standards
It ensures alignment with industry standards such as IATF 16949 and customer-specific quality benchmarks, which are critical for doing business in regulated sectors like automotive and aerospace.
3. Enhanced Supplier-Customer Communication
PPAP promotes structured communication and mutual accountability between manufacturers and their suppliers by establishing standardised documentation and expectations.
4. Continuous Improvement
The PPAP process provides a foundation for ongoing process evaluation and refinement, fostering a culture of continuous improvement across the organisation.
5. Stronger Audit Readiness
With complete and standardised documentation in place, PPAP facilitates smoother internal and external audits, reducing the risk of non-conformances and improving organisational credibility.
Quantitative Impact of Poor PPAP Execution
Failing to manage PPAP effectively can have severe cost and compliance implications:
According to a study by Automotive News, 30% of delayed vehicle launches are attributed to supplier part approval failures.
A report by McKinsey & Co. found that quality-related recalls cost global automotive OEMs over $45 billion between 2010 and 2020—many traceable to part non-conformance.
Deloitte’s 2023 manufacturing insights show that 70% of Tier 1 suppliers cite PPAP documentation errors as a top reason for rework or shipment delays.
These figures underline the necessity of digitising and standardising PPAP workflows to avoid disruption and preserve customer confidence.
Challenges in Managing the PPAP Process
Despite its structured approach, managing the PPAP process comes with real-world hurdles—especially when handled manually or through disconnected tools.
Manual documentation errors
Using spreadsheets and email often leads to incorrect data entry, missing fields, or outdated files—causing rework and approval delays.
Revision tracking issues
Without version control, teams struggle to track updates across documents, leading to confusion and misaligned submissions.
Delayed approvals
Poor communication and scattered workflows result in bottlenecks, slowing down approvals and extending production timelines.
Audit compliance gaps
Missing or inconsistent documentation puts companies at risk during audits, affecting customer trust and compliance scores.
Lack of system integration
When PPAP isn’t integrated with ERP or PLM platforms, teams face data silos, duplication, and poor traceability.
These challenges not only slow product launches but also raise compliance risks—especially for manufacturers relying on outdated methods.
Common Pitfalls in PPAP Implementation
Even experienced manufacturers encounter pitfalls in managing PPAP, especially when processes are fragmented:
Incomplete Submissions: Missing one or more of the 18 required elements is a common reason for rejection.
Misunderstood Customer Requirements: Failing to address customer-specific needs often leads to resubmissions.
Uncalibrated Checking Aids: Submitting inspection tools without up-to-date calibration documentation raises red flags during reviews.
No Change Control Mechanism: Updates to design or processes not reflected in PPAP documentation can result in audit failures.
Over-Reliance on Manual Tracking: Excel-based tracking lacks audit trails and introduces human error.
How to Streamline the PPAP Process
To reduce delays and eliminate compliance risks, forward-thinking manufacturers are adopting digital PPAP workflows that bring structure, automation, and real-time visibility into the approval process.
Here’s how organisations can streamline their PPAP operations for greater speed and accuracy:
1. Use document templates to standardise submissions
Predefined templates ensure all PPAP submissions follow a consistent format, minimising errors and omissions. Standardisation also helps suppliers meet customer-specific requirements without repeatedly starting from scratch.
2. Automate version control to track updates
Digital systems automatically manage document revisions, eliminating confusion over outdated files. This ensures that stakeholders always access the latest version, reducing rework and approval delays.
3. Route approvals through digital workflows with role-based access
Automated workflows assign tasks to the right individuals based on roles, preventing bottlenecks. Notifications and escalations ensure that approvals move quickly while maintaining accountability and traceability.
4. Integrate with ERP systems to pull real-time part data
Connecting the PPAP system with ERP platforms allows automatic data sync—like part numbers, supplier info, or production status. This reduces manual data entry and ensures accuracy across systems.
5. Store submissions in a central repository for easy audit retrieval
A cloud-based document repository provides a single source of truth for all PPAP elements. It simplifies audit preparation, enables instant search, and ensures version history is maintained.
By digitising the PPAP process, organisations not only enhance compliance and traceability, but also reduce approval cycles, improve supplier collaboration, and accelerate time-to-market—a competitive advantage in fast-paced manufacturing environments.
End-to-end workflow automation
Build fully-customizable, no code process workflows in a jiffy.
PPAP Readiness Checklist
Use this checklist to ensure your PPAP submission is accurate, complete, and audit-ready:
PPAP Submission Readiness Checklist
- Latest Design Records and Engineering Drawings approved
- DFMEA/PFMEA completed and reviewed
- Control Plan and Process Flow Diagram aligned with manufacturing steps
- All Measurement Systems analysed and verified (MSA)
- Material and performance test records available
- Qualified lab certifications included
- Sample parts and Master Sample tagged and labelled
- PSW signed and reviewed by all stakeholders
- All documents named and version-controlled properly
- Internal review completed prior to customer submission
Real-World Use Cases of PPAP in Action
PPAP is not just a theoretical framework—it’s actively implemented by global manufacturing leaders to ensure quality, consistency, and compliance in their supply chains.
The following examples highlight how top organisations apply PPAP standards to validate parts, streamline processes, and maintain traceability across complex production environments.
1. Ford Motor Company
Ford employs PPAP, including Level 3 submissions, to validate supplier components. Their Global Phased PPAP process mandates that suppliers submit required documentation, such as control plans, for safety and regulatory components across various submission levels, including Levels 1, 3, and 5.
2. Bosch
Bosch integrates PPAP processes across its automotive and industrial divisions. The company utilises SAP systems to manage quality and logistics processes, ensuring supplier submissions meet both internal and customer-specific requirements. For instance, Bosch’s integration of SAP Service Cloud with SAP ERP supports efficient billing and logistics, providing service agents with comprehensive visibility into order and shipping statuses.
Tools Commonly Used for Managing PPAP
While Cflow offers a flexible and no-code approach to automating PPAP workflows, many manufacturers also use industry-specific tools to manage documentation and quality control:
Teamcenter (Siemens PLM): Offers advanced document control and engineering change management integrated with PPAP workflows.
MasterControl QMS: Used in medical and pharma manufacturing to handle PPAP and FDA compliance simultaneously.
SAP Quality Management (QM): Integrated with ERP systems to manage inspection lots, test results, and PPAP documentation centrally.
Arena PLM (PTC): Cloud-based PLM with supplier quality collaboration features for PPAP submissions and audits.
These platforms support scalable, integrated PPAP workflows, especially in heavily regulated or high-volume manufacturing.
How Cflow Simplifies and Automates the Production Part Approval Process (PPAP)
Cflow is a no-code workflow automation tool that helps automate and streamline the Production Part Approval Process (PPAP). While not a dedicated PPAP platform like traditional PLM or QMS systems, Cflow’s flexibility makes it highly effective for managing and digitising PPAP documentation, approvals, and collaboration workflows.
1. Automated Document Workflows
Build workflows to route PPAP elements—such as Process FMEA, Control Plans, and PSWs—to relevant stakeholders (quality, engineering, procurement) for timely review and approval.
2. Template-Driven Submissions
Standardise and simplify submissions with custom forms for each PPAP element, minimising errors and ensuring all required data is captured.
3. Role-Based Access Control
Restrict access based on user roles to maintain data integrity, enhance security, and support audit-readiness.
4. Version Control & Audit Trails
Track document revisions, approvals, and history automatically—essential for traceability and IATF 16949 compliance.
5. ERP/PLM Integration
Seamlessly integrate with ERP or PLM systems to auto-populate forms with part numbers, BOMs, and supplier data, eliminating manual entry.
6. Centralised Repository
Store all PPAP submissions in a searchable, centralised location for easy access during audits or customer reviews.
7. Notifications & SLA Tracking
Automate alerts, reminders, and escalations to ensure timely approvals and avoid process bottlenecks.
If you’re still managing PPAP through spreadsheets or email chains, Cflow delivers structure, speed, and compliance—ideal for managing multi-supplier or global workflows.
Conclusion
PPAP is a vital process for maintaining quality and compliance in highly regulated manufacturing sectors. Businesses that fail to adopt a structured approach risk costly delays, failed audits, and reputational damage. With workflow automation tools like Cflow, manufacturers can take control of the PPAP process, reduce errors, and accelerate approvals. Start streamlining your PPAP documentation and approvals—Start a free trial of Cflow today to see how effortless compliance can be.
FAQs
1. Why is PPAP important in automotive manufacturing?
Because vehicle safety and performance depend on part reliability, PPAP ensures each component meets design, quality, and performance standards before production.
2. Can PPAP be used outside of the automotive industry?
Yes. While it originated in automotive, PPAP is now used in aerospace, defence, medical devices, and other regulated manufacturing sectors.
3. How long does a typical PPAP approval take?
The timeline varies depending on submission level and product complexity. With digital workflows, approvals can be completed within days instead of weeks. Automate your workflows with our Cflow experts.
What would you like to do next?
Get your workflows automated for FREE